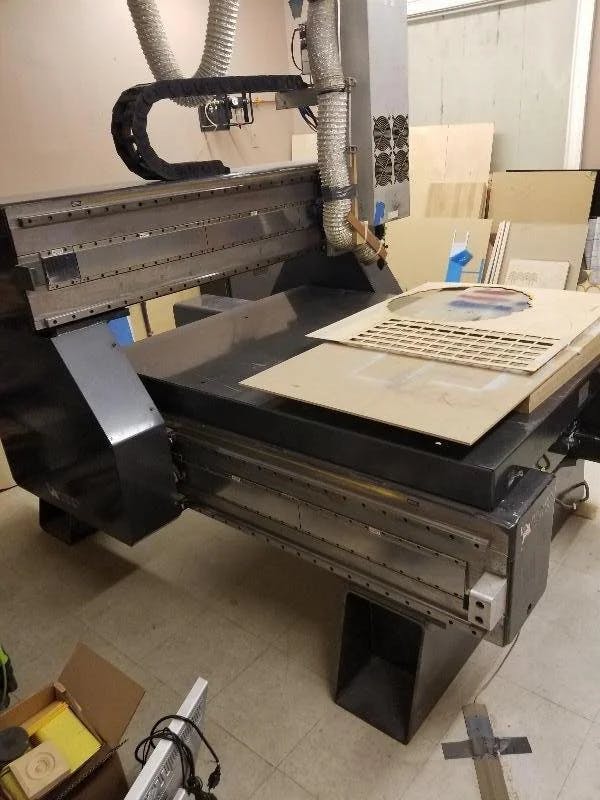
Comprehensive Insights into Laser Cutting Manufacturing Techniques
Introduction
Laser cutting is a precision manufacturing process that has revolutionized the way various materials are cut and shaped across a multitude of industries. Using a high-powered laser beam, laser cutting technology enables the precise and efficient cutting of materials such as metal, plastic, wood, fabric, and more. This process is guided by computer numerical control (CNC) systems, allowing for intricate and complex designs to be executed with remarkable accuracy.
The fundamental principle behind laser cutting involves focusing a concentrated beam of light, typically a laser, onto the surface of the material to be cut. The intense heat generated by the laser melts, burns, or vaporizes the material, creating a clean and precise cut along the desired path. The speed, intensity, and focus of the laser beam are carefully controlled to achieve the desired cut, making laser cutting a highly versatile and adaptable manufacturing technique.
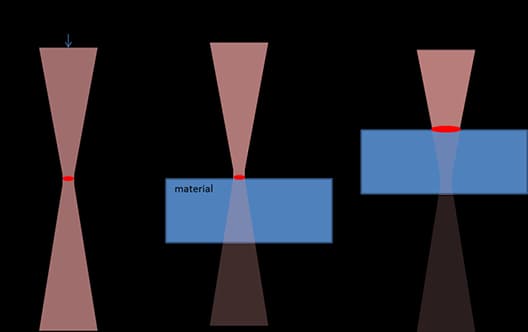
Laser cutting offers numerous advantages over traditional cutting methods, including high precision, minimal material waste, quick production speeds, and the ability to cut intricate patterns or designs. This process is widely utilized in industries such as automotive, aerospace, electronics, fashion, signage, and many others, contributing significantly to the advancement and innovation in modern manufacturing. In this introduction, we will delve deeper into the various aspects of laser cutting manufacturing, exploring its applications, benefits, machinery involved, and the overall impact it has on the manufacturing landscape. Delving into advanced laser cutting manufacturing techniques and their wide-ranging applications reveals the transformative impact of this technology.
Laser cutting involves utilizing a focused, high-intensity laser beam to cut or engrave a variety of materials, ensuring exceptional precision and speed. Controlled by computer numerical control (CNC), this process guarantees accuracy and repeatability, making it highly suitable for intricate designs and detailed cuts.
Key Advantages:
Micron-Level Precision: Laser cutting achieves extraordinary precision, crucial for intricate designs. Swift Processing: The laser beam enables efficient material processing, enhancing overall manufacturing speed. Material Versatility: It can cut a broad range of materials, from metals to plastics.
Types of Laser Cutting
CO2 Laser Cutting : CO2 lasers, using a gas mixture, excel in cutting non-metallic materials like wood and acrylic.

Fiber Laser Cutting : Fiber lasers, powered by solid-state laser sources, efficiently cut various metals, including steel and aluminum.
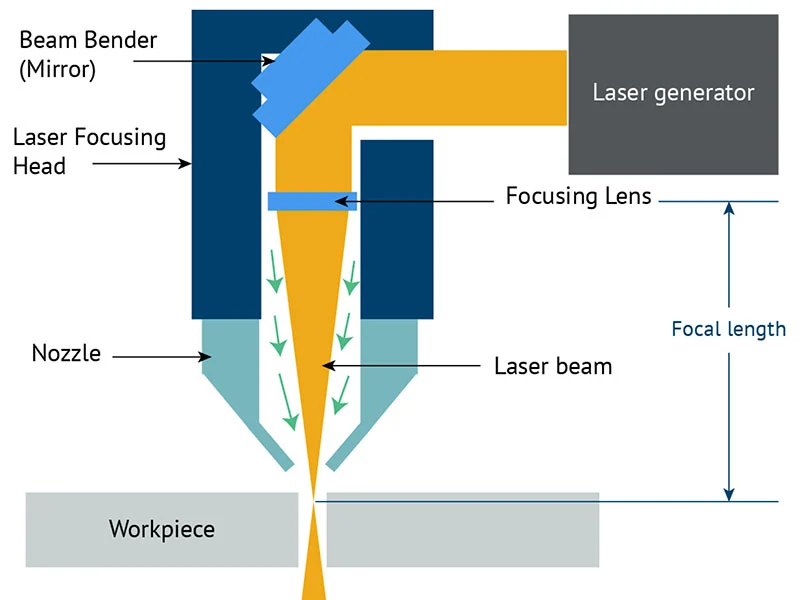
Nd : YAG Laser Cutting : Solid-state Nd:YAG lasers are ideal for cutting thicker materials and highly reflective metals.
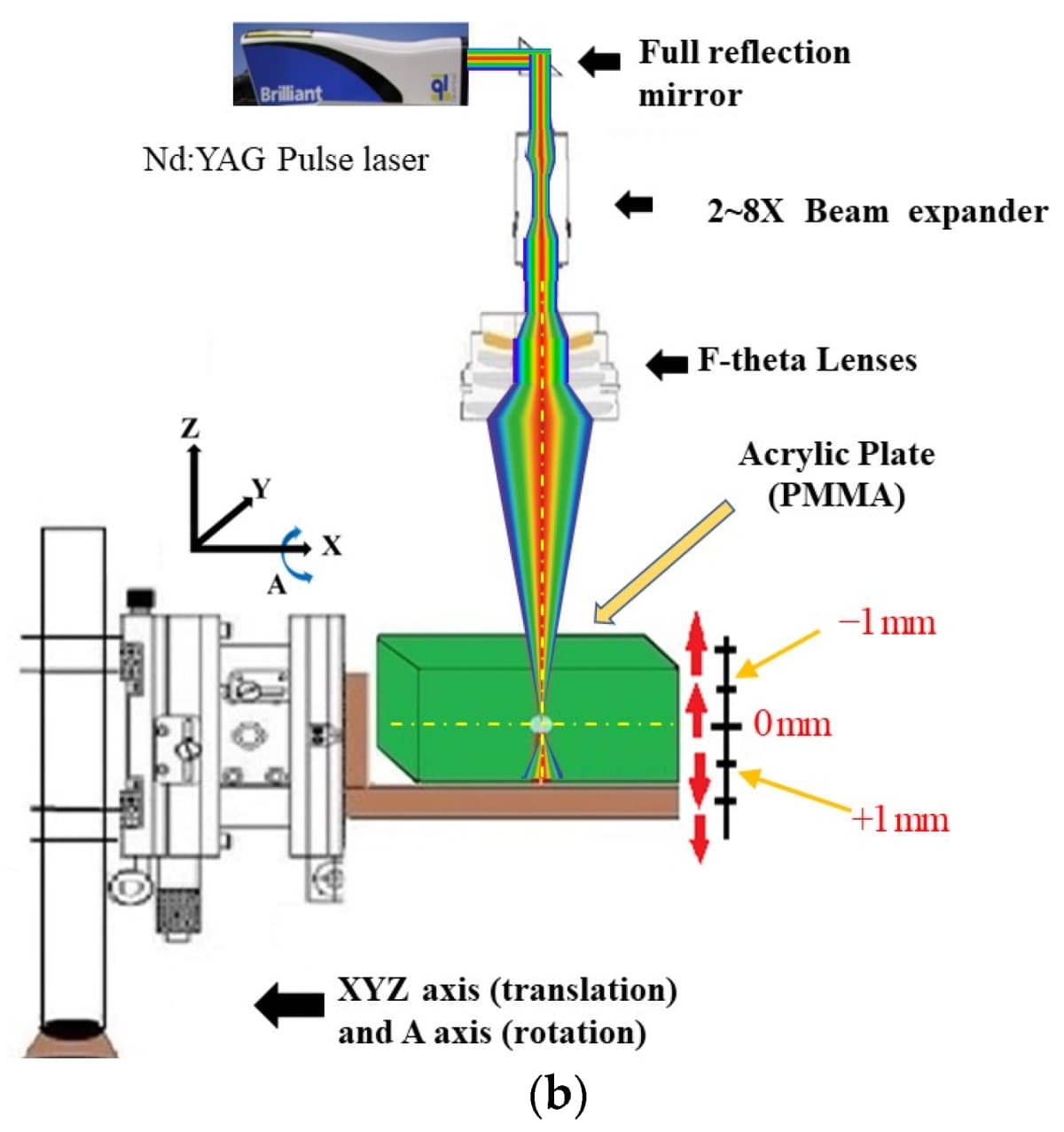
Key Advantages : Material Adaptability: Different laser types cater to specific materials, optimizing performance. Efficiency: Fiber lasers, in particular, offer high efficiency and cost-effectiveness.
Advanced Techniques and Innovations
Laser Microjet Cutting : Laser microjet cutting combines laser and water, enabling precise cutting of delicate materials with reduced thermal stress.
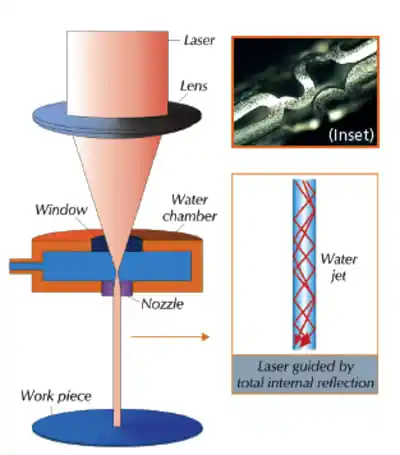
Laser Fusion Cutting : Laser fusion cutting involves melting the material with the laser and using high-pressure gas to remove molten material.
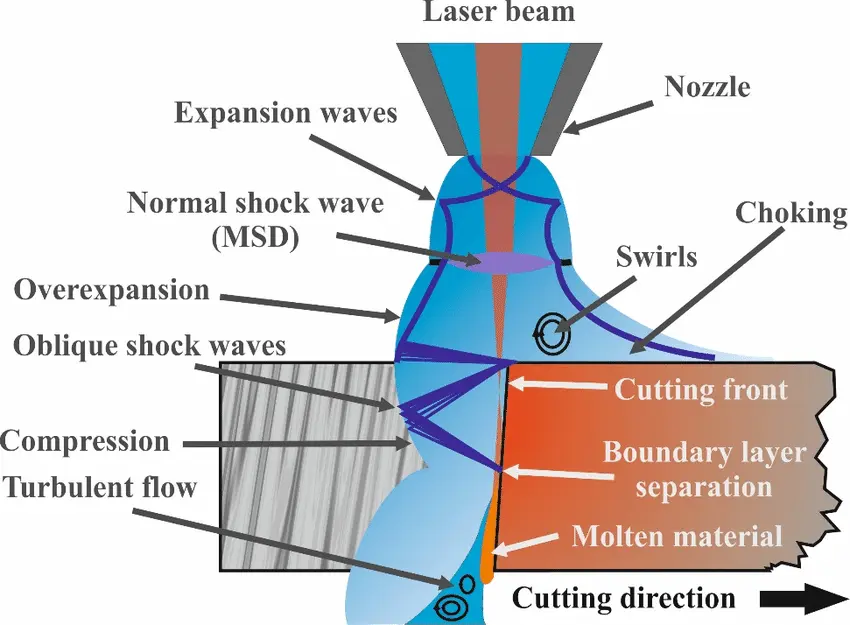
Key Advantages:
Enhanced Edge Quality: Advanced techniques provide superior edge quality and reduced thermal distortion. Optimized Speed and Accuracy: These techniques result in faster cutting speeds and increased accuracy. Advanced Laser Cutting Techniques
Credits
Advances in Laser Materials Processing and Applications
Conclusion
The continuous evolution of laser cutting technology revolutionizes the manufacturing industry, enhancing precision, efficiency, and adaptability. Manufacturers in Hyderabad, India, and worldwide can achieve exceptional results across various applications by staying updated on the latest advancements in laser cutting.
For further inquiries or expert assistance with laser cutting techniques, reach out to our team at contactus@mekuva.com